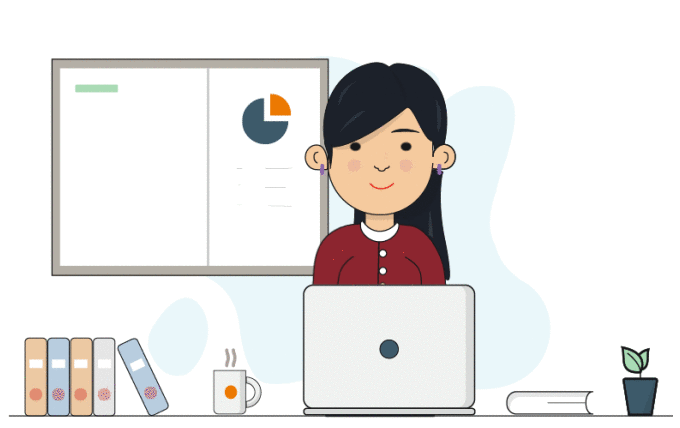
Total Productive Maintenance (TPM)
ZERO LOSS … an objective that any Growing Competitive and best in class company would Strategize. Are you one?
TPM is one of the proven impactful strategies implemented to drive Optimal efficiency, Waste reduction, Labor productivity, Employee and product safety, Product Quality, Employee and Customer satisfaction; all through Cultural Transformation resulting in Profitability and increase in Sales Revenue.
TPM is a ZERO LOSS and Sustainability Journey encompassing equipment reliability, workplace Safety, product quality driven by all employees’ engagement and sense of ownership.
TPM will provide the workforce with tools, and build their capabilities to drive results with Consistency (Daily Management Systems) , Creativity and Curiosity ( Continuous Improvement.)
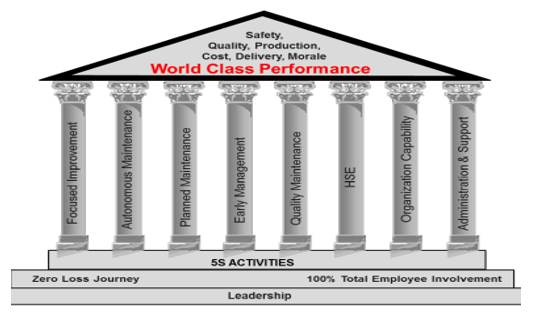
-
-
- Autonomous Maintenance
- Planned Maintenance
- Focused Improvement
- Organization Capability
- Early Management
- Quality Integration
- Health Safety Environment
- TPM in administration
-
Predicted Gains
TPM has both proven technical results and cultural results:
➤ TPM is expected to improve productivity by 35%,
➤ OEE from 50-70% to 80-90%,
➤ Reduce unplanned downtime by 80%,
➤ Reduce Quality defects by 50%.
➤ Reduce safety Lost Time Injuries and Recordable incident rates to zero
➤ The cultural transformation expected is having proactive, committed, and motivated teams working in a safe environment.
Our Methodology
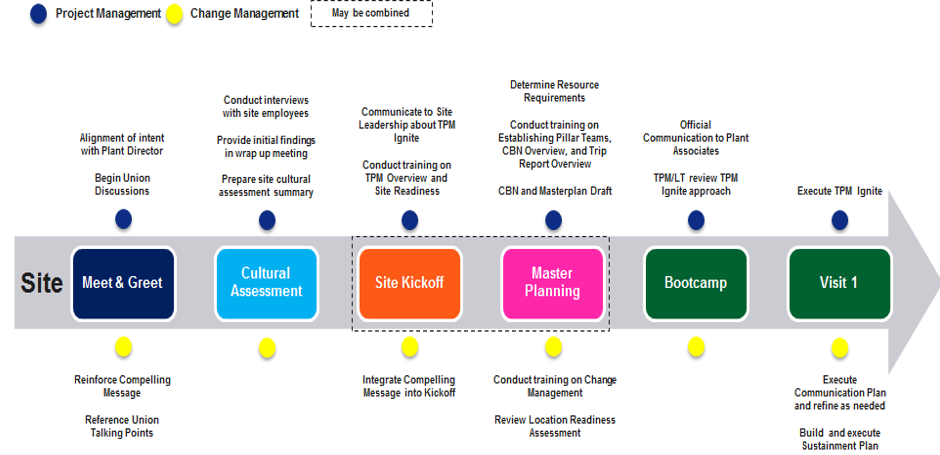
Featured Clients Story
CASE
Chools team collaborated with a 500 fortune Food & Beverage Company in North America to improve Overall equipment efficiency, reliability and productivity and establish a strategy that would ensure transformation and sustainability of results.
ACT
Our consultants guide the team in establishing TPM by adopting a TPM Ignite program:
- Starting with building the capability of the team through conducting a TPM overview training-( Leadership team followed by senior management and workforce .)
- Conducting a cultural assessment to identify the opportunities from an employee perspective.
- Build A Y chart- Compelling Business needs – based on SWOT with the leadership team to identify the Vision, Mission, and goals of the organization (Master Planning event).
- Assist the organization in selectin the pillar teams.
- Conduct detailed assessment and training for each pillar team – Bootcamp.
- Continue with monthly visits guiding the pillar teams in identifying opportunities, setting an improvement plan and execution strategy and providing them with the proper tools for this.
✔ Autonomous Maintenance: AM ACCELARTE, CILT, CL, 5S
✔ Focused Improvement: DMAIC and problem solving
✔ Organization Capability: Total Employee Involvement
✔ Planned Maintenance: Spare parts Management, Breakdown analysis, 5S , Preventive Maintenance, CMMS.
✔ EHS: Establish subcommittees: Working at heights, contractor management, LOTOTO, confined spaces, ergonomics.
✔ Early management: V Curves, Vertical start ups and CQV.
✔ Quality Management: ISO9000, HACCP , 3D Quality.
Result
➤ Across one year the Organization achieved
➤ 15% improvement on OEE,
➤ Zero Safety injuries and LTIR, RIR
➤ 10% productivity savings out of total base spend reflecting by 7% on $/case.
➤ 40% improvement on Labor productivity Cases/EE-HR.
Total Productive Maintenance (TPM) - Case Study
Problem –
A world famous and premier IT company has been looking to find a way out of paperbound processes. Digitizing their core entity, by removing all paper bound processes was their end goal. Operation administration was working with manual data collection, a process that wasted paper and printing material. The data encoding that was done so far was error prone, as typographical errors done through manual data encoding was a regular issue that the company had to deal with. Integrating a new software for Production Management that increased efficiency was conceived.
Solution –
The new solution helped the company on many fronts. From human resources to inventory management. The software solution could be used all over the organization.
It provided –
➤ Accurate calculation of timelines, and effective resource utilization.
➤ The software solution was mobile. Production plants in multiple countries were using the same solution as the one used in the parent company’s plant.
➤ The entire process of production control was taken care of by the solution.
➤ Everything from material input, order in-take by clients, production procurement, production lead-time estimation and quality control was handled by the software.
➤ Human resource management was made easier, making for efficient staff profiling, attendance, and salary/compensation database.
Result –
Fast processing and a very low rate of error, made it the perfect solution for the needs of the company. The employees were now enabled with the tools to work at full capacity in many different areas of management. They were able to run production on-time, depending on the requirements of the clients. Raw material usage could now be tracked accurately, which gave the company efficient raw data on manufacturing and stocking needs, depending on the needs of production.
Problem –
An FMCG company that specializes in machined components and fasteners, the company was looking for ways to implement TPM methodology in their production plants.
The study was conducted to see the various ways TPM methodology could be implemented.
A questionnaire was developed, which was swiftly circulated across the workforce, recording problems and feedback. Major losses incurred during production, wastage, and elements that hindered quality of product were identified using time study and statistical analysis.
Some of the problems they identified were.
➤ Defects in final product.
➤ Low production rate.
Solution –
Solutions for the main problems that were identified include –
➤ Roller die pressure, Roller Speed and Material hardness. Several levels of testing, ranging from high to low, were conducted on these three, which directly affected the quality of the final product. A series of design experiments were conducted by taking two and three levels of factors. Complete factorial design was conducted afterwards on the response variable.
➤ The second issue was resolved by giving due importance to increase in production rate. It was found that the low production rate was directly due to the larger cycle time for each operation. Cutting, Chamfering, Grinding and Threading. They were earlier conducted on separate machines. But when the traub machine was studied, it was found that it had provisions for special attachments, which reduced the number of processes by 3.
Result –
Over the course of this exercise two levels of improvement were made possible. Both quality improvement and product improvement. These were done by properly implementing the principles of TPM, to improve both utilization of equipment and utilization of manpower.
TOTAL PRODUCTIVE MAINTENANCE – TEMPLATES
1. TPM – TOTAL PRODUCTIVE MAINTENANCE
2. TOTAL PRODUCTIVE MA INTE NA NCE
3. THE 5S CONCEPT
4. TPM RUNNING EFFICIENCY &TRUE EFFICIENCY
5. TPM – MAINTENANCE PILLAR
6. ABNORMALITY MANUAL
7. TPM – PRACTITIONER
8. CAPABILITY MATURITY MODEL
9. TPM OVERVIEW
10. TPM – ESTABLISHING PILLAR TEAMS
11. LEAN MANAGEMENT
TOTAL PRODUCTIVE MAINTENANCE – SHEETS
1. OVERALL EQUIPMENT EFFECTIVENESS
2. INSTRUCTIONS
3. CAPABILITY ANALYSIS
4. CALENDAR
5. RISK ASSESSMENT
6. CHECK LIST
7. CHECKLIST – MAINTENANCE
8. PREVENTIVE MAINTENANCE CHECKS AND SERVICES