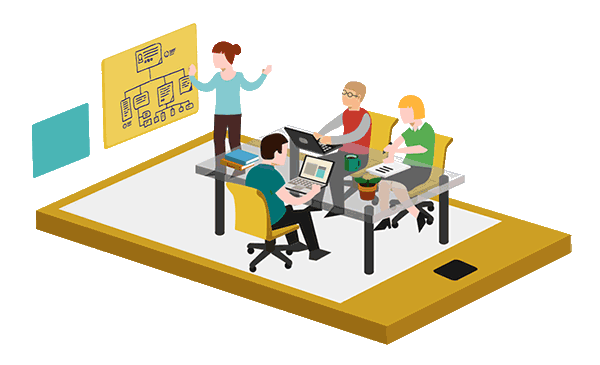
“Change for the better”
The Japanese word “Kaizen” is a brilliant concept that helps to improve work practices of people from multiple departments.
Kaizen is a business philosophy of continuous improvement. Kaizen promotes change through teamwork and collaboration. It brings all the ideas and inputs together from the different departments and levels of the organization.
Chools Consulting:
with their hands-on-expertise in facilitating Kaizen events, are sure to help your business improve the operations and increase productivity. In facilitating a Kaizen event, our team of experts are sure to ensure a work environment that is more efficient, by motivating employees to work as a team, engaging the employees and thus making the job less tiring and more effective.
A Kaizen initiation must be done by the following sequence of events:
Targeting the process:
The initial step in initiating Kaizen is to be sure about the outcomes and goals that the organization aims to achieve from the process improvement. The processes are reviewed through data analysis to arrive at a clear picture of the current state of the operations.
Developing the team:
It should be ensured that all the people, the departments, their functions that affect the operations, are clearly outlined. One representative from each department ought to be included in the event. This is done so that there is equal representation from all departments in giving inputs before a change is brought into effect.
Scheduling the Event:
At this stage it becomes imperative that the Kaizen event is brought into effect without affecting the normal functioning of the other processes. During the event, teamwork is the linchpin. Members should be mindful in appreciating inputs from all the staff.
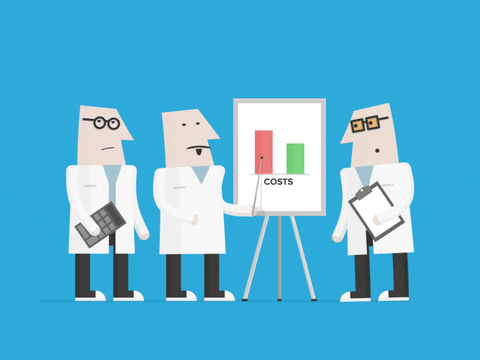
Sequence of the Kaizen event: Once the Kaizen event is initiated, it must flow through the following timeline.
➤ A detailed sketch of the existing processes, the steps, the flow of information through the processes, and how they interact with one another is drafted.
➤ Identifying the operations where time is lost and where there is no value added to the goal.
➤ Assessing if the customer would be willing to pay for that step or process.
➤ Elimination of waste by removing unnecessary tasks, reducing the time on the process, and value addition to the end user.
Drawing up the conclusions:
The final step in the Kaizen initiation will be drawing the sketch of how the future process would look like. This is done after the change has been approved on the consent of all the team members.
Documentation of changes:
Once the Kaizen event is completed, the new processes thus agreed upon shall be documented and circulated to the remaining members of the organization to be accepted as the new standard process. The smooth implementing of the new process depends on the collective efforts of the members. After the event has gone live in the organization, to validate the changes incorporated, data is collected and compared, to monitor improvements.
Coming together is the beginning of new things.
Schedule a Kaizen event with Chools Consulting. We will be there with you through out the journey to empower your business towards operational efficiency!
Kaizen events - Case Study
The Challenge
A major food manufacturing company with recognizable brand value was affected by waste getting accumulated in the production line that was negatively impacting the productivity.
The Background
With two decades of operations in the food manufacturing business, the company was seasoned in marketing its product to customers and the established businesses. They had a well-formed channel and distributed through retail outlets, website and wholesale businesses. Its recent COO had gone through Lean Transformation program and had a clear idea about the company’s production process. He was aware of the human and the material resource waste and the negative impact it had on the bottom line.
The Lean Transformation
➤Chools conducted an extensive two week Kaizen event. It was a rapid improvement program designed for identification and fixation of individual problems. Nine member cross-functional team was dedicated to evaluate the current process and design a new solution to balance the line.
➤With conventional Lean Transformation approach, we started with ways to process the waste followed by the performance of multiple time studies on the current production line. The new process options were practiced with mock-ups and test runs. The Kaizen team tested the process with multiple iterations. The final phase of testing was carried out by the company’s complete first shift.
➤The new process worked exceptionally well. The very next day the second shift went live. To ensure the sustained success of the process, we came up with the idea of line lead person to monitor the flow and daily management along with the execution of the process and addressing the problems.
The Outcome
We were able to relocate a significant number of people to other areas of the organization where their help was crucial. Two new leadership positions were created, the remaining team had new career path options. In addition to balancing the line, the utmost positive outcome was the savings worth thousands of dollars concerning material costs.
The Background
A prominent manufacturer was concerned regarding significant production delays and late customer shipments regarding his organization. When the delays occurred, sales staff would make a sincere effort to expedite the orders in possible circumstances. But they often ended up apologizing to the customer for being unable to meet the committed order delivery dates. This inevitably caused sales to decline.
The Solution
Chools conducted a diligent investigation. It was found out that the entities responsible for causing the concerning delays were scheduling, warehouse picking, calibration and final assembly. Chools suggested a series of targeted Kaizen events to be run with the addressed departments. It super-headed the process of developing end-to-end solutions. It addressed the root causes of the issues. With sincere compliance, Lean awareness training was delivered to a significant number of employees in hundreds.
The Results
The order delivery was stabilized. Expediting was greatly reduced. The need for customer notification on order delays was eliminated. The implementation of layout improvement and the single-piece flow methods led to the outcomes resulting in inventory reductions and shorter lead times.
1. KAIZEN
2. 5S IMPLEMENTATION PLAN
3. KAIZEN – CYCLE
4. KAIZEN – ACTION PLAN
5. KAIZEN – PDCA CYCLE
6. KAIZEN – PDCA