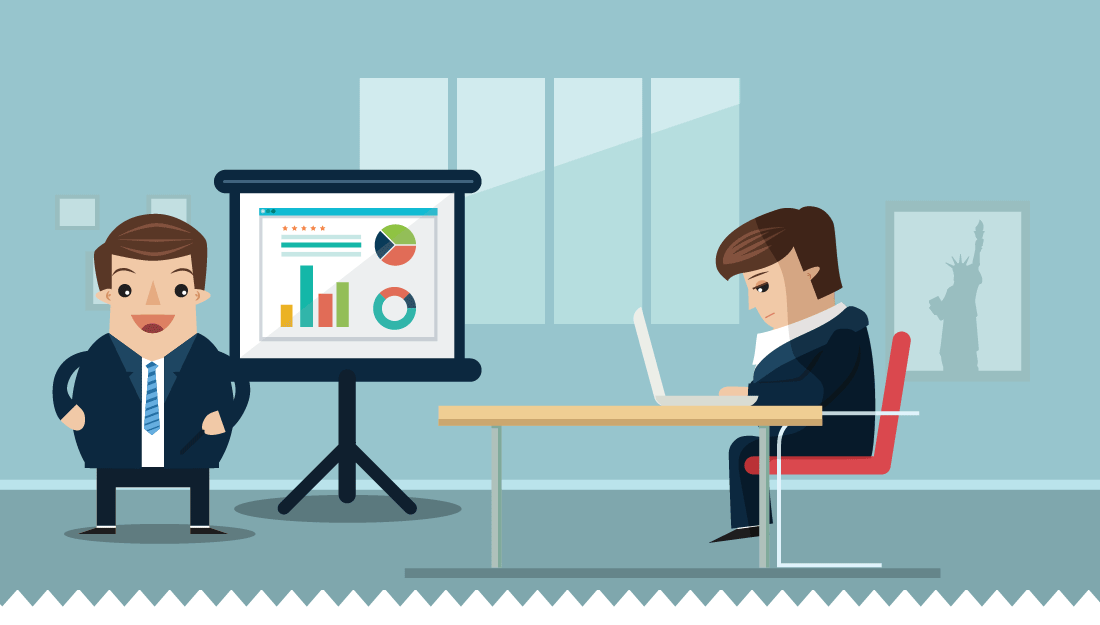
Operational Excellence – PITSTOP
PITSTOP is also known as SMED is a Focused Improvement tool that will create breakthrough results in your Profitability and Operational Excellence journey achieved through Overall Equipment Efficiency losses elimination. In addition to Lean Tools use, our consultants will investigate all Changeovers, Cleaning, and Sanitizations events/practices via various types of assessments: Time Studies, Motion studies, Ergonomics assessments, 5S audits, process parameters measurements, video recordings, employee diagnostic and skills assessments – integrated with the DMAIC methodology to reveal optimizing opportunities to:
➤ Reduce Setup times
➤ Reduce Impact of those non added value processes to drive improvement of line Efficiencies and Capacity Utilization
➤ Increase Operating flexibility
➤ Gives capability for shorter runs and thus less inventory and more floor space
➤ Reduce Material Handling
➤ Increase operator capability, efficiency, and Safety.
➤ 3-5 Points-% improvement on production line OEE.
➤ > 90% Line Capacity Utilization.
➤ Standard Work & Continuous Process Flow.
➤ Equipped, Engaged and Empowered Workforce.
➤ Automation Solutions and Interfaces.
Our Methodology

Define
✔ Problem Statement : Gap to targeted OEE and utilization caused by C/O – CIP
✔ Business Impact and Benefits
✔ Team and Scope
Measure
✔ $ Value for 1 OEE Over heads /Line costs
✔ Tiime/Motion studies – capture all current process steps
✔ Identify Internal , external, non added value steps
✔ Study Process Parameters ( CIP, temp, flow rate)- (C/O fittings, equipment subcomponents)
✔ Employee Diagnostics- Skill assessments
✔ Line As -Is Audits – 5S
✔ Video recording
Analyze
✔ Brainstorming , Nominal Group Technique
✔ Problem solving Techniques: FMEA, 8D, 5 whys,BDA, FISHBONE
✔ Gap Analysis- Current OEE VS Glide path
✔ Effort /Impact Matrix , SWOT
Improve
✔ Eliminate non added value steps and convert internal to external
✔ Generate ideas for 5S – Motion – Ergonomics improvements
✔ Simplify fittings and installations and optimize parameters
✔ Reduce time of adjustments and trials
✔ Standard Work Strategies
✔ Vertical Startups -VSU
Control
✔ Create Balanced Scorecards for tracking
✔ Workforce Training
✔ Visual Controls , Centerlines -Andon , Poka-Yoke, Jidoka
✔ SOPs
✔ MES/ERP — Data Capturing

Related Case Study

Case : Chools was hired by 100 fortune Food and beverage company in MEA Region to drive and develop its Productivity, Lean Six sigma, performance and TPM journey. CIP and QCO PITSTOP was one of the methodologies used to drive OEE Improvement.

Act : Chools Consultants conducted pitstop across 8 plants – 16 production lines. Our consultants inside the DMAIC methodology used the various assessments and several Lean problem solving and analysis tools and above all trained the team.

Results : An annual Increase of 10% OEE points was realized for the region, this translated to $3.8MM – 3.7% of Manufacturing Base spend.
Savings captured encompassed all MOH ; Labor utilities , Maintenance and operating supplies costs.
SMED– PITSTOP - Case Study
Problem
A Leading Beverage producer with an annual NOPBT of $40MM Partnered with Chools to improve the overall equipment efficiency on their production lines. One of the biggest opportunities was identified as a Size Change over ON ONE OF THE Cans lines that takes 12 Hrs impacting the OEE by a loss of 11% /Yr . The OEE was 71%, short from the annual operating plan by 9%.
Solution
After looking at the historical Data, we conducted a Pitstop event to measure all tasks and analyze with the line crew the opportunities and improvement plan. The following was identified
✔ Optimize scheduling to reduce number of Changeovers through improving forecast accuracy measure.
✔ 5 tasks could be externalized.
✔ Utilization of resources to assist in the Machine Changeover that took the longest time.
✔ Using automatic tools that reduce the time of redundant tasks: Bolts /screw tightening using an automatic Gun, automatic Filler and labeler crank for heights adjustments.
✔ 5S Changeover parts and Tools to reduce Motion and waiting during the changeover.
✔ Introduce Quick Change over parts.
Elimination of 2 Non added value steps in inspecting the cans after seaming.
New process was tested and standardized and crew trained on.
Results
The Changeover time was to 2.7hrs decreasing the Impact of the changeovers on OEE from 11% to 3%. This reduced the $/Case of the cans line by 20%. Moreover, introducing the new changeover tools reflected on employee morale and safety related to ergonomics.
Case
A Leading Juice producer hired Chools to improve the overall equipment efficiency for their production lines. One of the biggest opportunities was identified as a Cleaning in Place (CIP) activity on their Highest volume PET Line. The CIP took 5 hours vs. a standard of 2 hours benchmarking with other affiliates This had an impact of 6% Loss on OEE. The OEE was 75%, short from the annual operating plan by 6%.
Solution
After looking at the historical Data, we conducted a Pitstop event to measure all tasks and analyze with the line crew the opportunities and improvement plan for the CIP activity, which consists of 5 steps (Cold CIP, Hot CIP, Chemical Sanitization, Cold CIP, External Cleaning). The following was identified
✔ Optimize scheduling to reduce number of CIP through improving forecast accuracy measure.
✔ Optimize sanitization Matrix.
✔ Modify Piping diameters to increase flow and decrease time.
✔ Optimize temperature of Hot water cleaning step to reduce waiting time for getting filler Hot, which also influenced Fuel and water consumption.
✔ Reduce time of steps validated by Quality team.
✔ Eliminate first Cold step cleaning.
✔ Conduct external cleaning in parallel to last CIP step through installing water nozzles on filler.
Results
The CIP Time was reduced from 5hrs to 2hrs, and number of CIP events were reduced from 156 to 78 times per year. The Loss on OEE contributed by CIP for this Juice line was reduced from 6% to 2%. The $/case for that line and SKU was reduced by 17%. In addition, Water consumption was improved by 11% and Fuel consumption by 5%.
1. PITSTOP
2. KAIZEN SMED
3. PRIORITIZE REQUIREMENTS
4. PITSTOP OPERATIONS
5. KAIZEN SMED FORMS
6. TIP FOR DELIVERING
7. ANNUAL OPERATING STRATEGY
8. PROVEN WAYS TO INCREASE YOUR SERVICE VALUE
9. PITSTOP STEP OF ACTIONS
10. PITSTOP TRAINING CHANGE OVER
11. PITSTOP TRAINING
12. PITSTOP PROCESS OVERVIEW
13. PITSTOP ANALYZE
14. PITSTOP THE 5 STEP PROCESS
15. STORE ROOM METRICS
16. SMED STORE ROOM STANDARDS
17. MAINTENANCE SKILL GAP
18. PITSTOP OVERVIEW
19. LUBRICATION MANAGEMENT
20. POWER TRANSMISSION
21. CO-ORDINATING MEETING
22. WORK ORDER PROCESS