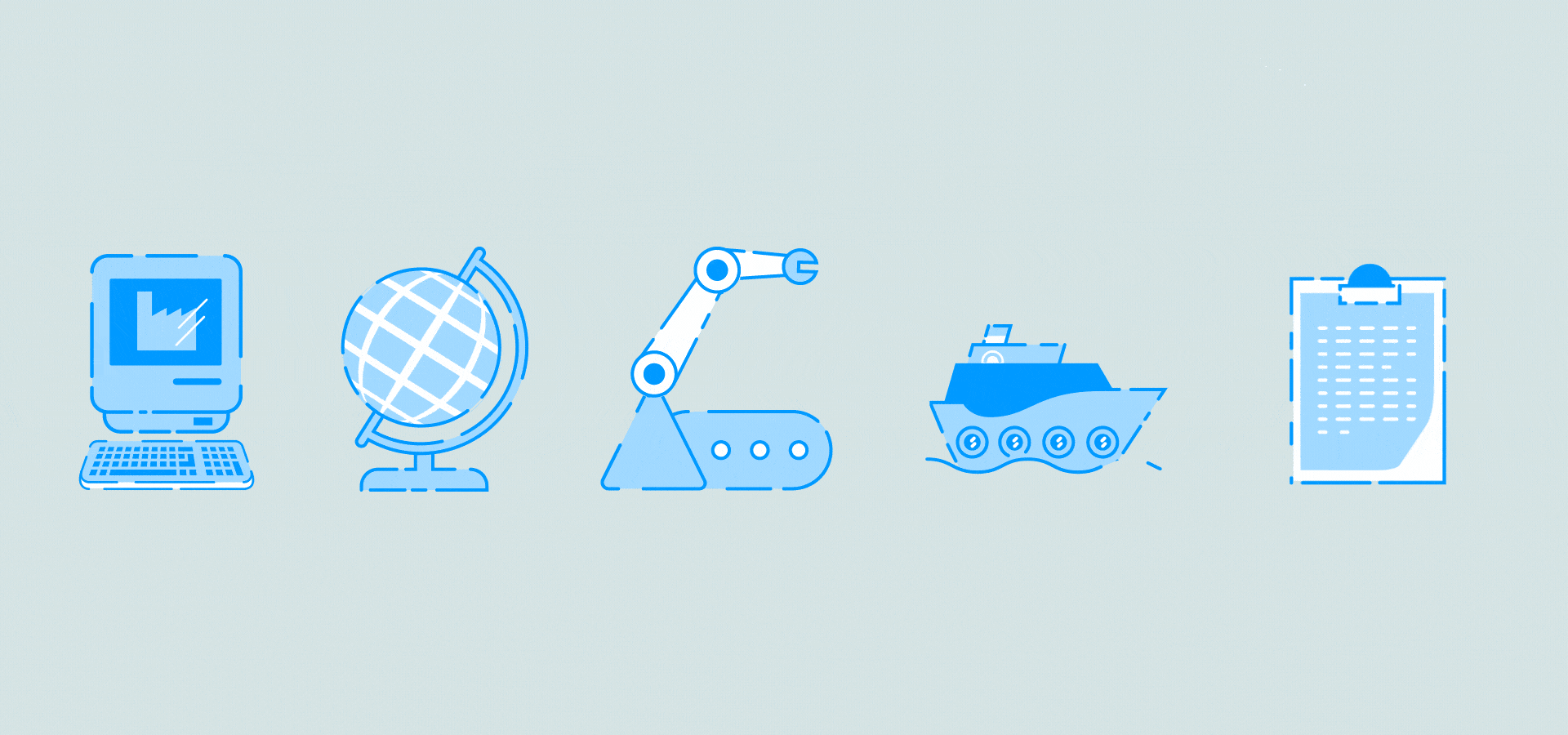
Boost Agility Speed & Efficiency: BASE
Learn and apply Agile-Lean-Six-Sigma (ALSS) tools and techniques to improve any business process, while getting certified as White-Belt, Yellow-Belt, Green-Belt, Black-Belt. The ALSS courses build robust skills in opportunity analysis and project management to deliver measurable impact. As an ALSS student, you will learn how to uncover hidden potentials and systematically drive performance improvements, creating real benefits for you and your company. Over the past 20 years, we have trained over 30000+ champions in 40+ countries who delivered over $500 million hard savings from their first Agile Lean Six Sigma projects alone. Start applying proven tools and techniques to ‘move the needle’ of relevant key performance indicators (KPIs).
➤ Kick-start your professional improvement journey
➤ 100% online, self-paced, with certification exams
➤ Get certified as a White, Yellow, Green, Black Belt
➤ Eliminate wastes and boost efficiency with Lean
➤ Accelerate project implementation with Agile
➤ Reduce variability to boost quality with Six Sigma
➤ Translate opportunities into formal project charters
➤ Take quizzes to check your knowledge, get feedback
➤ Apply learning to create measurable improvements
➤ Standardize processes and create work instructions
➤ Deliver real benefits by reducing effort, time, cost
➤ Download ALSS toolkits and ready-to-use template
Why You Want It
➤ Build skills to boost your career by simultaneously improving quality, speed, productivity, and cost. Your will learn how to apply problem-solving and performance-improvement techniques to create breakthrough results for your process, team, and company.
➤ The training helps you to reduce waste and complexity with Lean to improve flow and efficiency, eliminate the causes for variations and defects with Six Sigma to boost quality and customer satisfaction, and accelerate improvements with Agile through incremental, iterative project delivery.
➤ Agile Lean Six Sigma courses are for mangers and functional specialists to reduce variations and defects by up to 90%, measurably increasing productivity, cost, quality, and customer satisfaction with a return on investment of 10x. Nothing to lose, much to gain. Boost skills and results now!
White Belt Topics
➤ 8 Wastes Identification
➤ 5S Method and Audit
➤ Fishbone 6M Categories
➤ 5 Why, simple Problems
➤ PDCA Process, Template
Quotes from course participants:
➤ “I can see things clearly now”
➤ “This is totally common sense”
➤ “The impact of your coaching on my life has been massive”
➤ “Everyone should learn this”
➤ “I’m getting back in control”
➤ “A new way of working”
➤ “This was practical and fun”
➤ “Why haven’t we thought about this before?
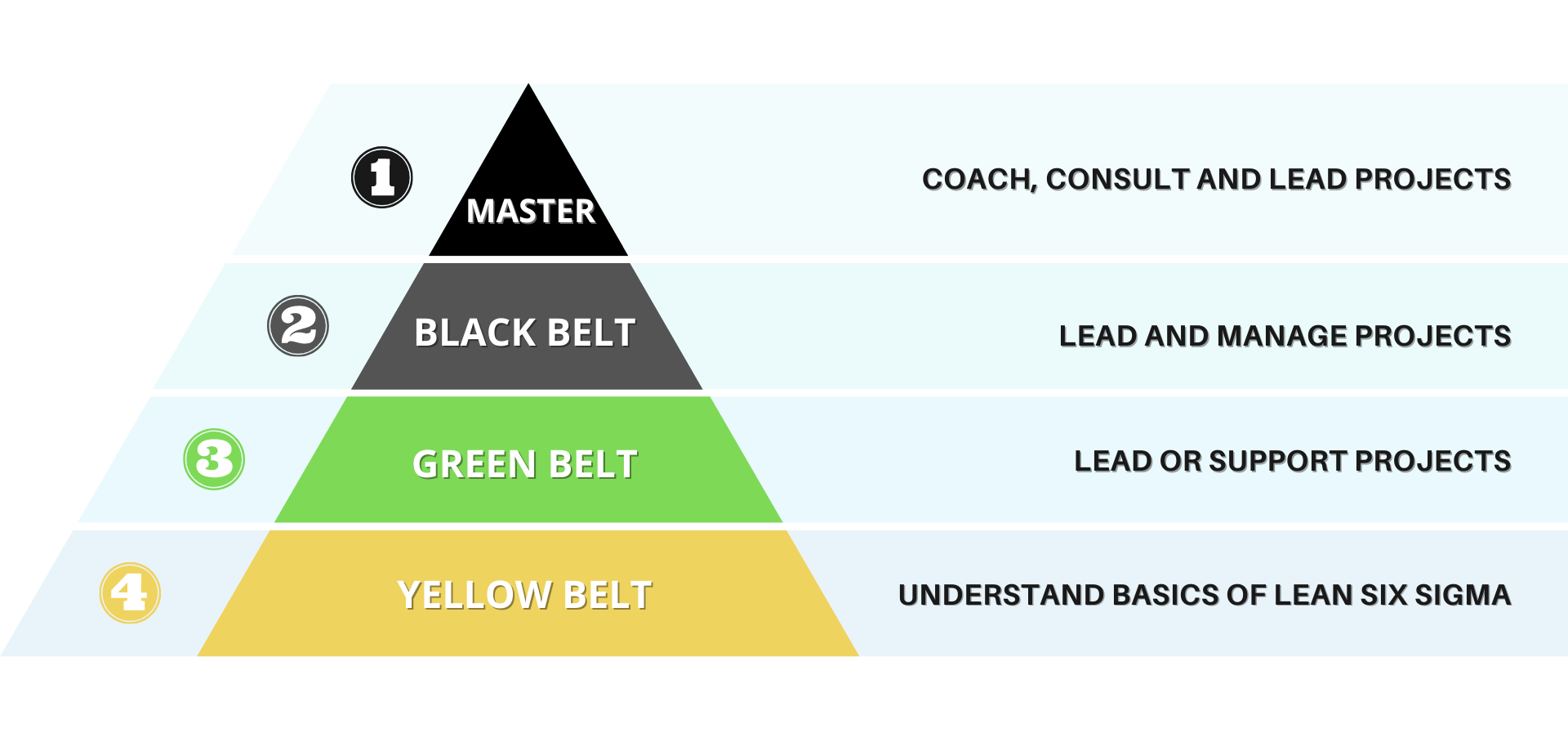
Yellow Belt Topics
➤ Agile Project Charter
➤ 5S as a System
➤ 8W “DOWNTIME”
➤ Basic Control Charts
➤Abnormality Signals
➤ Batch and Queue
➤ Cellular Concept
➤ Continuous Flow
➤ Cycle Time Basics
➤ Downtime and Efficiency
➤ Error-Proofing, Poka-Yoke
➤ First-In First-Out FIFO
➤ Fishbone Ishikawa 6M
➤ Kaizen Principles, Project
➤ OPL One Point Lesson
➤ Overproduction
➤ Problem Solving PDCA
Green Belt Topics
➤ Agile Sprint Planning
➤ Daily Scrum, Sprint Review
➤ Cycle, Takt, Tact, Pitch
➤ Inventory Optimization
➤ Just-in-Time JIT
➤ Lean Manufacturing
➤ Lean Admin & Service
➤ Load-Leveling, Heijunka
➤ Management Boards
➤ Product and Service Matrix
➤ Pull Systems: A and B
➤ Setup Reduction SMED, RTS
➤ Skill-Matrix
➤ Spaghetti Chart
➤ Standard Operating Procedure
➤ Total Productive Maintenance
➤ Value Stream Mapping VSM
Black Belt Topics
➤ Product Roadmap Creation
➤ The 7 Quality Control Tools
➤ Cost of Poor Quality COPQ
➤ Profit Per Hour PPH
➤ Zero-Based Budgeting ZBB
➤ Flexibilizing, Balancing
➤ Flow Production, Service
➤ Non-Performance Cost NPC
➤ Process Capability Cp, Cpk
Black Belt Topics
➤ Measurement System GR&R
➤ Pull Systems: A, B, C
➤ Risk Analysis FMEA
➤ Strategic Planning, Roadmap
➤ Strategy Deployment, X-Matrix
➤ Cycle Time, Takt, Pitch
➤ Yield FPY, FTY, RTY
➤ Variability Reduction Method
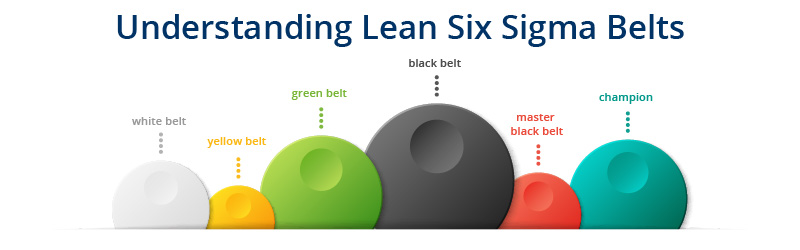
Lean Six Sigma – Program Brief
How it works:
The program consists of three parts: training, application, certification. During the training, participants learn about principles, tools, and techniques. Right after the training, they apply learnings in practical improvement projects to build real skills and create measurable benefits.
How long it takes:
The time to become a White Belt takes 2 days effort over a 1-month period, a Yellow Belt takes 5 days effort over 2 months, a Green Belt requires 10 days effort during 2 months, and a Black Belt is certified after implementing a transformation program, requiring at least 30 days effort over a 6-month period.
Who is involved:
The four key roles are sponsor, student, trainer, and controller. The sponsor initiates the program, provides context and allocates resources. The student invests time to read the material, complete the exercises, develop a project, and implement improvements. The trainer reviews progress and provides coaching feedback. For Yellow Belt and above, the project controller validates financial benefits created.
What you can expect:
Certified Lean Six Sigma champions are able to see and act on opportunities that were not known or not addressed before. By improving quality, efficiency, and flexibility, those champions generate real benefits from reduced defect rates, faster delivery, lower cost, and higher customer satisfaction.
How much it costs:
Courses generate a positive return as skills are applied and improvements implemented. Most projects achieve full payback within the implementation period, delivering a financial benefit 10x over tuition fees (ROI), making it a worthwhile investment
White Belt
➤ Purpose: build certified capability at the «Advanced» level for managers and specialists, responsible for teams or assets.
➤ Schedule: 10 days effort within a 3-month period to learn the theory, implement a cross-functional improvement, and attain certification.
➤ Exit competencies: map value streams, implement flow and pull, apply statistical analysis and controls, solve advanced problems, train and certify White and Yellow Belts.
➤ Benefit: cross-functional project to deliver at least 20% performance gain and $20,000 financial benefit.
Yellow Belt
➤Purpose: build certified capability at the «Intermediate» level for anyone working with a computer, machine, or process.
➤ Schedule: 5 days effort within a 2-month period to learn the theory, implement a small improvement project, and attain certification.
➤ Exit competencies: improve process quality and efficiency by reducing wastes, develop project charters, solve basic problems, train and certify White Belts.
➤ Benefit: functional improvement to deliver at least 10% performance gain or $5,000 financial benefit.
Green Belt
➤ Purpose: build certified capability at the «Advanced» level for managers and specialists, responsible for teams or assets.
➤ Schedule: 10 days effort within a 3-month period to learn the theory, implement a cross-functional improvement, and attain certification.
➤ Exit competencies: map value streams, implement flow and pull, apply statistical analysis and controls, solve advanced problems, train and certify White and Yellow Belts.
➤ Benefit: cross-functional project to deliver at least 20% performance gain and $20,000 financial benefit
Black Belt
➤ Purpose: build certified capability at the «Expert» level for program leaders and organizational change agents.
➤ Schedule: 30 days effort within a 6-month period to learn the theory, implement a transformation project, and attain certification.
➤ Exit competencies: lead cross-site transformation programs, apply statistical methods to analyze and solve complex problems, train and certify White, Yellow, Green Belts.
➤Benefit: transformation project to deliver at least 30% performance gain and $50,000 financial benefit.
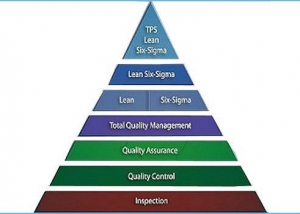
Skill Pyramid
The Skill Pyramid is a professional support structure that allows people to connect with each other, exchange experiences, develop new ways of working, and provide expert knowledge and coaching support. For example, a customer service agent who is working on a Yellow Belt project receives support from an accountant, who is a certified Green Belt and worked on a similar project before. Leanmap helps clients to design and implement such professional support structures that leverage expert-skills across functions, divisions, and sites. As Master Black Belt (MBB) or Project Management Officer (PMO) we provide interim management assistance to ensure that the program delivers the desired change and impact .