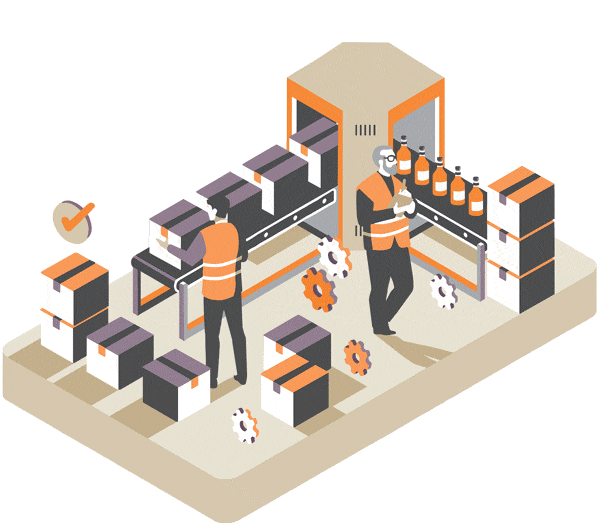
Customer Satisfaction, Product Differentiation and Waste Reduction are all factors and strategies to achieve higher Profitability. One of the Basic Prerequisite scheme to ensure achieving those strategies is executing Good Manufacturing Practices.
Good Manufacturing Practices
Good Manufacturing Practices (GMP) principles guide Fast manufacturing consumer goods industries; most importantly, Foods, Beverages, and Drugs; ensure their consumers are Safe, and satisfied by the Usefulness and Quality of the product. GMP apply to all aspects of your industry starting from Suppliers and sourcing to production and packaging to delivering the products to the Market and Customer, including logistics and transportation, and is a pre-requisite for other advanced programs : HACCP , ISO2200, SQF,IFS. GMP are monitored and audited by FDA, therefore, GMP is inevitable for the continuity of your operations.
CHOOLS consultants and competent team will Assess and establish a GMP execution and auditing program to Ensure your compliance with GMP Guidelines
The following will be covered:
✔ Manufacturing operations
✔ Processing Equipment and utilities
✔ Raw Materials and suppliers
✔ Packaging processes
✔ Physiochemical and microbiological Laboratories
✔ Building and supporting Facilities
✔ Waste water plants
✔ Waste disposal and recycling processes
✔ Chemical, Physical, Environmental and Health Safety Hazards analysis and prevention.
✔ Personnel training
✔ Product Recall Processes
✔ Documentation and Records
✔ Consumer Complaint Records and tracking.
✔ Quality and Food safety Key performance measures monitoring.
✔ Labeling process.
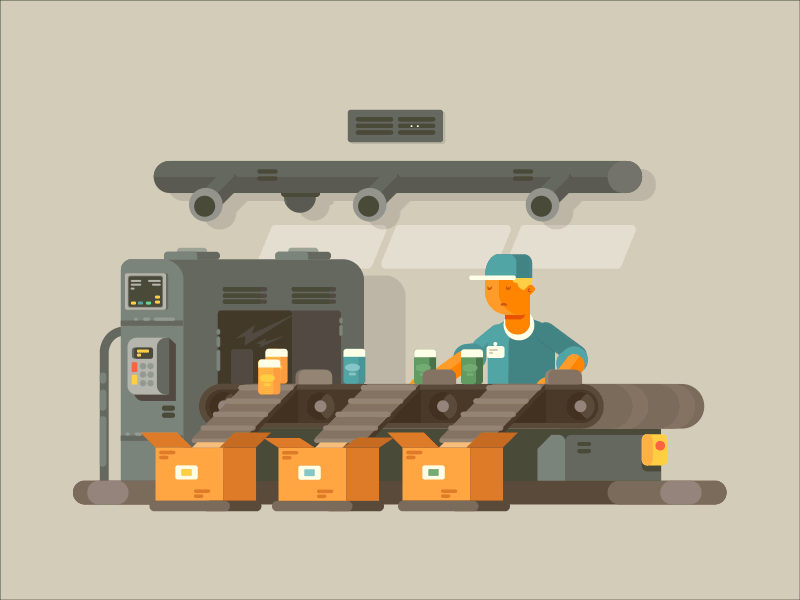
Predicted Gains
The primary gains that you will capture form GMP:
➤ Increase Productivity through Waste Reduction
➤ Increase Market Share through Customer Satisfaction and product reliability.
➤ Compliance with regulatory requirements
➤ Consistency, Control, Accuracy, Reconciliation and traceability through proper documentation and labeling.
Our Methodology
➤ Assess the Current Business, Operations and Processes including documentation, suppliers, building and facilities, the whole value chain.
➤ Build the Good Manufacturing Practices program that complies with the minimum required regulatory standards to ensure Compliance and commitment to producing safe products, including supplier management and Customer complaints response.
➤ Build the proper daily management and auditing system to increase operational efficiency, streamline processes and eliminate non-complaint activities.
➤ Qualify the team for attaining HACCP or ISO22000 certification.
Good Manufacturing Practices - Case Study
CASE
Chools team collaborated with a Food Manufacturing Startup company in the Middle East to prepare them for FDA annual Audit and ensure their compliance with the required regulations.
ACT
➤ Our consultants guide the team in establishing the proper GMP guidelines customized to the Entity operations, putting a Daily Management system and program of execution and auditing. We started with a Gap analysis to report the status versus the desired status. GMP related to all Value chain starting from suppliers, Raw material receiving an inspections and storage to processing and packaging to storage, loading and transportation of product to market was established.
➤ Microbiological and physiochemical testing to ensure health safety of product was in place. Required inspections, testing, documentation, SOP’s for each process was established. Pre-requisites such as 5S, Supplier approval and qualification system was established.
➤ Period for establishing the program robustly was three months followed by monitoring and auditing services for effective execution and consistency and for building the capability of the team.
Result
The company cleared the FDA audit but most importantly now has a solid GMP program that ensures compliance to health an Food safety, customer trust with the product, and waste reduction .
CASE
Extending the existing GMP program in a leading pharmaceutical company to HACCP ( Hazard Analysis Critical Control Point ) program. The company had three production lines, the HACCP started from receiving of Raw material, storage and inspection to processing and packaging and storage in coolers.
ACT
Chools team established process flow sheets for all production lines went through the analysis: Biological, Physical, Chemical, based on the severity and the occurrence identified the Hazard magnitude and Critical Control plan. This was followed by establishing the CCP control limits, Monitoring procedures, Corrective actions, Verification procedures and the records keeping and documentation. In addition, the Operational Prerequisites programs for all CCP’s were found.
Result
Establishing the HACCP and GMP program resulted in eliminating any risk of producing any product with a biological, chemical or physical Hazard that would put the customer at a health safety risk. Resulting also in waste reduction as the proper control measures and prerequisites programs for all critical control points were established.
1. INTRODUCTION TO THE TRAINING COURSES
2. BASIC PRINCIPLES OF GMP – QUALITY MANAGEMENT and PHARMACEUTICAL QUALITY SYSTEM
3. BASIC PRINCIPLES OF GMP – SANITATION AND HYGIENE
4. BASIC PRINCIPLES OF GMP – QUALIFICATION AND VALIDATION
5. BASIC PRINCIPLES OF GMP – COMPLAINTS AND RECALLS
6. BASIC PRINCIPLES OF GMP – CONTRACT PRODUCTION, ANALYSIS and OTHER ACTIVITIES
7. BASIC PRINCIPLES OF GMP – SELF INSPECTION and QUALITY AUDITS
8. BASIC PRINCIPLES OF GMP – PREMISES
9. BASIC PRINCIPLES OF GMP – EQUIPMENTS
10. BASIC PRINCIPLES OF GMP – MATERIALS
11. BASIC PRINCIPLES OF GMP – DOCUMENTATION ONE
12. BASIC PRINCIPLES OF GMP – DOCUMENTATION TWO
13. BASIC PRINCIPLES OF GMP – GOOD PRACTICES IN PRODUCTION AND QUALITY CONTROL
14. GMP INSPECTION PROCESS – INTRODUCTION
15. GMP INSPECTION PROCESS – THE ROLE OF THE INSPECTOR
16. GMP INSPECTION PROCESS – PREPARATION FOR THE INSPECTION
17. GMP INSPECTION PROCESS – TYPES OF GMP INSPECTION
18. GMP INSPECTION PROCESS – THE INSPECTION
19. LEAN MANUFACTURING
20. DEVOPS INFINITY
21. PRODUCT QUALITY MANAGEMENT in MANUFACTURING FIRM