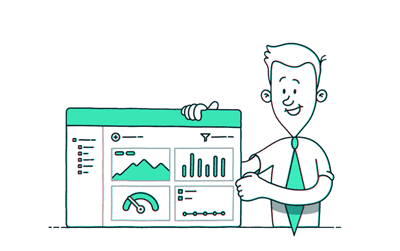
Advanced Product Quality Plan
With proper application, APQP establishes a firm relationship between customer and supplier. That relationship is derived out of strong confidence that exists concerning the quality of the product. Wrong application of APQP leads to disastrous consequences in the entire design process. The ultimate consequence inevitably will be a sabotaged relationship between the customer and the supplier.
Most well-known companies perceive APQP as a worthwhile substitute for the Product Development Process. The APQP process demands a rigorous and detailed approach to product development. Presence of a Cross-Functional Team (CFT) is the prime requirement. Organizations with supply chains performing critical tasks may positively benefit from implementing strategic approaches of APQP. With limited resources, accomplishing the task appears overwhelming, that’s when Chools comes into the picture.
➤ Chools APQP consulting is all about deep involvement. We first emphasize on understanding your overall product and your required process development. Completion of the initial analysis is followed by the development of time and cost-effective process.
➤ The two major aspects of APQP are significantly enhanced by our counsel. Preventing failure on the latest products of the organization. Followed by effective implementation of APQP deployment for the supply chain.
Chools Consulting Services builds APQP process foundation by defining and addressing the following aspects:
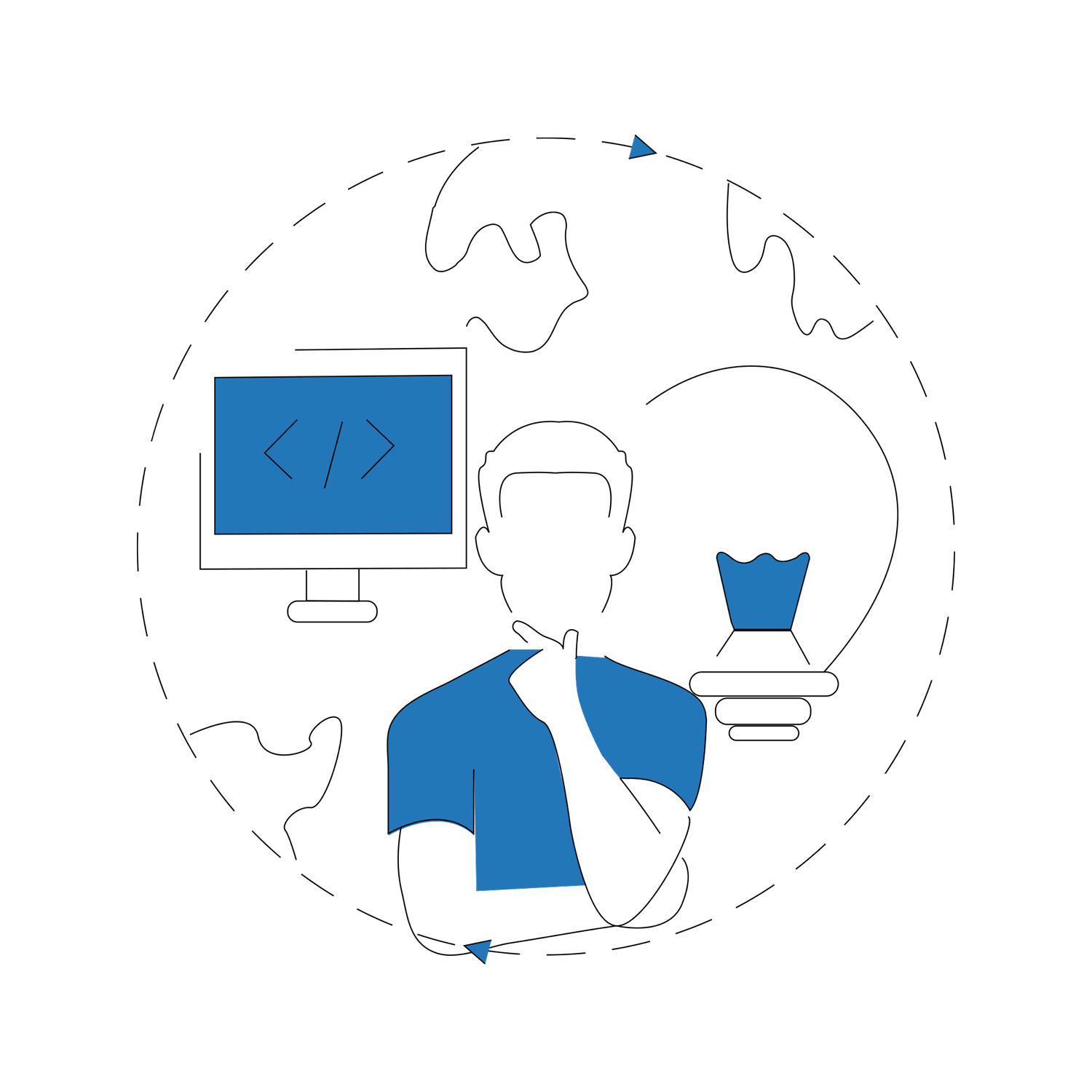
➤ Product Development.
➤ Required Resources.
➤ Avoiding past failures.
➤ Discovering failure modes early in PD.
➤ Developing Special Characteristics.
➤ Managing Design and Process Change.
➤ Collaboration in design of product and process.
➤ Appropriate APQP tool selection.
➤ Implementing systems and techniques for enhanced PD efficiency and efficacy.
➤ Apt APQP tool selection for capturing failure.
➤ Capturing future preventive actions.
The application of APQP holds prime importance for the supply chain. The supply chain support of an organization’s NPI is significantly improved with smart utilization of APQP. Additional considerations, critical for applying APQP to supply chain are:
➤ The accurate number of high value suppliers. Engaged and Managed.
➤ The value of supplier inputs important to product performance.
➤ The various levels of Production Part Approval Process (PPAP).
➤ Time required for satisfactory completion of APQP.
➤ Training and mentoring requirements for improvement of supply chain support.
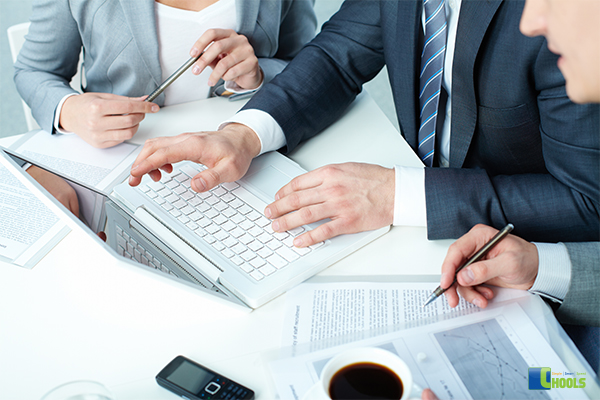
Developing an APQP methodology that is potent in quality and agile in process management is an outcome possible with reliable assistance from professional resource. Chools provides firm assurance with respect to creation of a world class APQP process that acts as a catalyst for your company’s product development process and as an adhesive for your relationship with your customers.
➤ The exclusive benefits you receive from a premium APQP consulting:
➤ Mesmerizing design experience for both your company and your customers.
➤ Complete integration of your requirements into your product from concept to customer.
➤ The notable tools used:
✔ Failure Mode and Effects Analysis (FMEA)
✔ Design for Assembly (DFA)
✔ Control Plan Methodology
✔ Design Review Based on Failure Modes (DRBFM)
➤ Enhanced collaboration between the major entities like product, process design, purchasing, supply chain and manufacturing.
➤ Systematic development of risk mitigation plans for prevention actions
➤ Product development cycles with increased speed.
➤ Advanced quality control systems and control plans
➤ Upgraded systems supporting product development, manufacturing and service.
➤ Supply chain engagement with careful consideration of time.
➤ Alignment of project goals with organization objectives.
➤ High priority placed on customer satisfaction. Significant reduction in warranty cost. Prevention of a full-fledged campaign.
Advanced Product Quality Planning - Case Study
Case
➤ A Computer chip Manufacturer got customer complaints and had to recall one line of products. The Manufacturer after analysis had to design a new part. The Manufacturer needed to improve their design process initially and approached Chools team for the consulting service.
Solution
➤ The team started analyzing the complaint and voice of customer including all requirements using QFD (Quality Function Deployment).
➤ Weekly design for manufacturing cycle and status meetings were established which took 6 weeks.
➤ In week 8 the manufacturing team reached a prove design order
➤ Week 10-22, three prove design iterations and testing were provided.
➤ Following that a PPAP process was established and executed (production part approval process)
➤ Finally, the product was produced successfully
Results
The Chip was designed successfully and tested by the customers for effective application.
Case
➤ A Growing beverage Manufacturer was expanding and the research and development function was targeting adding a new product to their portfolio. They wanted to achieve this through a APQP process to achieve the best design with less variability.
Solution
- First step was determining the customer needs and expectation using QFD and voice of customers through surveys and market research . It was identified that customers are looking for a healthy beverage with different fruity taste.
- Through the second step : Product Design and development; the customer inputs were analyzed and execution of outputs were planned using FMEA, DFMA, Material and engineering specification , design reviews and verifications and resources allocation and commitment.
- Design and development of process
- Process and product validation through process capability analysis, production testing, production control plan, product quality planning and PPAP sign off .
- Finally any corrective action and design change was done based on customer and market evaluation.
Results
➤ The product resulted in great success raising the sales revenue of the company by 7% and market share by 5%. The company is using the established APQP for introducing new products.
1. IMPROVING PRODUCT QUALITY IN MANUFACTURING
2. NEW PRODUCT – DEVELOPMENT, ANALYSIS and APPROACHES
3. PRODUCT DEVELOPMENT PHASE
4. PROJECT PRODUCT MANAGEMENT STATUS
5. APQP TRAINING
6. PRODUCT LIFE CYCLE
7. PRODUCT CANVAS
8. PRODUCT COST MANAGEMENT
9. PRODUCT MANAGEMENT